

Фирма «Лайл Хэндмейд Найфс» предпочитает сталь D2, несмотря на ее умеренную коррозионную стойкость, из—за способности хорошо держать заточку (на снимке изображен нож «Десвинд» — Deathwind, с клинком из этого сорта стали)
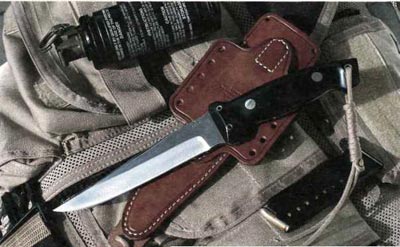
Уильям Харси во время шлифовки титановой стопорной пружины для складного ножа «A—F». По мнению мастера, клинок тактического боевого ножа должен быть выполнен из нержавеющей стали.
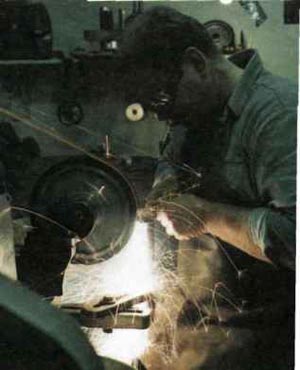
Аллен Элишевиц (Allen Elishewitz) большое значение придает способности стали держать заточку, поглощению вибрации и антикоррозионным свойствам, поэтому выбирает для своих клинков нержавеющую сталь 154СМ фирмы «Крусибл Стилз» (Crucible Steels), являющуюся аналогом японской стали ATS–34, причем мастер допускает использование ножей как в полевых, так и в городских условиях. Того же мнения придерживается мастер Билл Харси, также оценивающий сталь по ее антикоррозионным свойствам и способности держать заточку в экстремальных условиях. Под этими условиями мастер подразумевает, например, воздействие соленой воды во время использования ножа в морских операциях, когда клинок из—за коррозии становится тупым еще до того, как его вынут из ножен.
Поэтому он категорически против ржавеющих углеродистых сталей. Чтобы добиться оптимального результата при использовании стали 154СМ, которую он также очень высоко ценит, мастер строго соблюдает предписания относительно твердости металла. Он считает, что будущее — за порошковой сталью, способной хорошо держать заточку, но, по его мнению, такие сорта стали значительно повысят стоимость ножей. Мастер Боб Терзула, известный внедрением различных новшеств, также отдает предпочтение стали 154СМ. Он считает, что порошковая сталь по способности держать заточку имеет явное преимущество, но проблемы, возникающие при обработке, и более дорогой материал не стоят того, чтобы вкладывать в это большие средства. Сталь, уязвимая к ржавчине, как считает Терзула, не должна использоваться для изготовления складных ножей.
Абсолютно иную философию исповедует канадский мастер Уэлли Хэйес (Wally Hayes), предпочитающий углеродистую сталь 0–1. Преимущество он видит в возможности достижения селективной твердости клинка с гибким обухом и твердым лезвием. Структура металла лезвия, по его мнению, более мелкая, чем у нержавеющего сплава, что положительно сказывается на остроте лезвия. Чтобы ножи можно было использовать в морских операциях, он просто покрывает клинки слоем кальгарда. Это мнение разделяет Чарлз Оке, использующий для своих ножей также углеродистую сталь Е–52100. Стивен Дик (Steven Dick), главный редактор журнала «Тэктикал Найфс», также видит преимущества в отношении остроты лезвия на стороне таких сортов углеродистой стали, как А–2, G–1 или 1G95, правда, одновременно он указывает на то, что при недостаточном уходе клинки ржавеют.
На основе различных мнений можно сделать вывод: как углеродистые стали, так и нержавеющие стальные сплавы могут использоваться в качестве материала для изготовления клинков тактических боевых ножей. Оба вида стали, в зависимости от выполняемых задач и области применения, имеют как преимущества, так и недостатки, сравнить и взвесить которые необходимо самому пользователю.
Сплавы на основе кобальта
Сплавы на основе кобальта были разработаны для деталей авиационных турбин, испытывающих большие нагрузки и способных выдерживать, в первую очередь, предельные механические нагрузки, воздействие высоких температур и быть очень устойчивыми против коррозии. Речь идет о деформируемых сплавах с очень высоким содержанием карбида, где железо заменяется кобальтом. Материал имеет исходную твердость около 47 HRc, и повышать ее уже нельзя. За счет исходной твердости процесс обработки клинка очень трудоемок и стоит довольно дорого. Мастер Харольд Карсон назвал однажды этот сплав «пожирателем абразивной ленты». Преимуществом здесь является высокая износостойкость лезвия при работе с относительно мягкими материалами, такими, как мясо, дерево и тросы, кроме того, сплав отличается очень высокими антикоррозионными свойствами. Большие нагрузки в виде ударов могут создавать проблемы, так как при столкновении с твердыми материалами лезвие просто гнется, поэтому перед использованием необходимо предусмотреть те нагрузки, которые будет испытывать материал при выполнении той или иной работы. К самым известным сплавам на основе кобальта относятся стеллит 6К и талонит. За последние годы талонит активно использовал в производстве ножей мастер Роб Симоних (Rob Simonich). Одними из немногих промышленных фирм по изготовлению ножей, остановивших свой выбор также на этом материале, стали «Камиллус» и «T.O.P.S.» Отпускные цены на такие ножи выше, чем на аналоги, клинки которых сделаны из других сортов стали.

